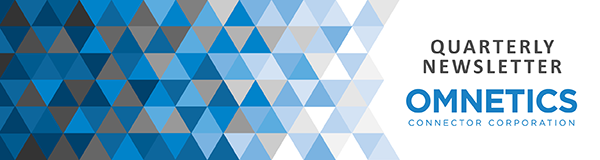
Nano-D Connectors
As technology evolves, bigger isn’t always better. Almost every technological product is becoming smaller and faster, including many products that use connectors. The small but mighty Nano-D is quickly surpassing its predecessor, the Micro-D, in popularity due to its small size and rugged design. Omnetics has seen product growth for the Nano-D in the following markets:
- Small Satellites
Because launching satellites into space can cost tens of thousands of dollars per pound, size and weight are the main objectives when designing connectors inside a satellite. Cube satellites and small satellites have grown in popularity along with the growth of Nano-D connectors. In a standard satellite, standardized printed circuit boards are stacked and electrically interconnected. Nano-D connectors are chosenfor these connections because of their versatile format and size. Retention screws are used to maintain signal integrity and long term mating in space, and Nano-D connectors use low outgassing materials that meet NASA specifications. Custom cable harnesses and flex circuits can be used to route signals between circuit boards.
- Phased Array Radars
Radars are used to detect enemy missiles, objects in the atmosphere, and anything else of note happening in the sky. These instruments send out a pulse of radio waves, and determinethe location of the object by watching what radio waves are reflected back. Traditional radars use only one beam of waves and measure the return waves by turning the main beam. Phased array radars, however, use an array of hundreds or thousands of beams to measure which waves are reflected back to earth. This allows the user to be able to keep a constant eye on their target, rather than waiting for the main beam to turn. These hundreds or thousands of signals need to be connected, which requires many pin connections from the edge of the radar transmit card to the focal beam circuit. Nano-D connectors with high pin counts are often used on the edge of the circuit boards within a phased array radar due to their small size and high durability.
- LIDAR Systems
Similarly to phased array radars, LIDAR (Light Detection and Ranging) systems also use high pin count Nano-D connectors to transmit data. LIDAR systems are used on UAV’s, helicopters, and airplanes to survey the ground using lasers. The system sends out pulses of light to determine the direction and distance from the ground below, giving the user a clear picture of the terrain. LIDAR is used to produce precise information about both natural and manmade environments, which is helpful in a wide variety of applications. To accomplish this, LIDAR instruments need circuit boards containing high-density connectors and small, flexible cabling. The Nano-D connector is optimized for this harsh environment.
With a .025 inch pitch (0.635mm), Nano-D connectors are only ¼ the volume of a Micro-D connector, and have 80% less mass. Nano-D connectors are specified to MIL-DTL-32139. Omnetics connects the wires to the pins and sockets using high pressure crimping technology, eliminating the potential problems of soldered leads coming into the back of the connector. Externally, the metal shells are constructed of aluminum alloy and nickel plated. Internally, the insulators are molded from liquid crystal polymer, allowing the connector to perform within a wide temperature range: -50 degrees centigrade to +200 degrees centigrade. Full specifications can be found here.
As instruments become smaller and their capabilities become greater, speed must increase as well. As signals are changing from analog to digital, circuit speeds are ramping above 2Gb/s and beyond 10Gb/s, and photon signal management is enhancing performance and protecting devices from cyber intrusion. When specified, cable signal speed capability and formats are designed to match the miniature Nano-D connectors. Designs available include IEEE 1394 fire-wire cable and expands to USB 3.1 formats and CAT-6a wiring. Higher speed data serial links can also be supported with smaller size cable and rugged Nano-connectors. Formats from USB 3.1, PCI Express 2.0/3.0, HDMI and others reaching up to 10 Gigabit Ethernet circuits are included. Contact Omnetics sales for more information.
Micro Strip Connectors
Omnetics’ Micro Strip connectors can transmit your electrical signals effectively and reliably in applications where size and weight are at a premium—and in today’s world, that’s usually the case. Micro Strip connectors from Omnetics are a premium choice when reliability is a top priority.
When engineers are designing their systems, they will often save designing in the connectors for last, leaving little space and weight for the connector. Omnetics Micro Strip connectors were developed and designed with that in mind, and product designers can be sure that they will find a connector that fits with their board, box, or any given space designated for a connector. Omnetics will be sure to design and build the .050” pitch connectors to minimize the space they take up based on the application’s signal, mating, latching, and mounting requirements.
Using the Omnetics Flex-Pin system that conforms to MIL-DTL-83513, you can be sure your Micro Strip connector will meet and/or exceed your stringent temperature, shock, vibration, and outgassing requirements. The gold over nickel plating of the pins and sockets makes for a highly reliable connection, and the mated pairs have been tested and proven to meet and exceed tough military requirements. The ruggedized liquid crystal polymer (LCP) insulators have been proven to hold up in tough environments as well. Operating temperatures, mating cycles, shock & vibration, and other electrical, mechanical, and environmental data is available online at our Micro and Nano Strips page.
Small satellite programs continue to use strip connectors from Omnetics in their systems. The combination of miniature size, reduced weight, and proven reliability encourage engineers to design their systems using Omnetics Micro Strip connectors where they need a reliable connection between boards or from board to box. They have been proven to handle the shock and vibration experienced during the launching of a satellite, and Micro Strip connectors have favorable outgassing properties for when the connectors are in space. Adding latches or retaining screws to the connector increases the connector’s volume by a minimal amount, while assuring the connectors stay mated during harsh environments.
Omnetics Micro Strip connectors come in single and dual row configurations, with the option of offset rows that reduce the overall height, all at .050” centers. Micro Strip connectors come with the option of adding latches, guide posts, mounting holes, retaining screws, along with all sorts of application-specific offerings. Omnetics’ website also has a product configurator tool to input number of signals, tail types, and mating & mounting requirements. The configurator will then produce a 3D model to easily incorporate into the system. Requesting a drawing from Omnetics is just as easy. A specific part number will be created and a 3D model can be requested as well.
Omnetics’ manufacturing line is established to allow virtually limitless configurations of our strip connectors. The LCP housings are molded, and then secondary machining operations can add latch slots, mounting holes, retaining screw features, and guide post holes. You can configure your specific connector to make sure you are saving space and weight while maintaining signal integrity and durability. Omnetics offers many types of tail terminations, and our Flex-Pin system can crimp to all types of wires, from 24 to 32 AWG. If signal integrity and speed-related performance are required, twisted pairs and cable shielding are options to consider.
From the Engineer’s Desk: High Speed Connector Design
Cable Design: Selecting the Right Shield for Your Application
In our series on Cable Design, this installment will discuss selecting the right shield for your cable.
Introduction
The cable shield is a conductive material that surrounds wires inside a cable. The purpose of a shield is to prevent noise from disturbing the signals within the cable and its surrounding environment. There are two different types of shields within cables: an individual shield, around a single twisted pair to prevent crosstalk inside the cable, and an overall shield, around the entire cable bundle to prevent electromagnetic interference (EMI) from radiating into and out of the cable bundle.
Key Considerations
There are several parameters that should be considered when selecting a cable shield:
- Shielding Effectiveness measures the shield’s ability to prevent EMI. Can also be described as “percent coverage.”
- Flexibility has a significant impact on the compliance of the overall cable.
- Flex Life determines the ability of a cable to withstand flexing throughout the life of a cable.
- Low Resistance ensures that shield can mitigate low frequency signals.
Shielding Options
The various shielding options, shown in Figure 1, are described below.
- Foil shields have excellent shielding effectiveness – up to 100% in many cases – and is very thin which can lead to excellent flexibility. The downsides are the poor flex life and the high resistance.
- Braided shields have good flexibility, flex life and low resistance. However, they are not ideal for high frequency applications as it is impossible to achieve 100% shielding effectiveness. Typical braid coverage is between 80% and 95%.
- Foil and Braided shields provide the best of both worlds and is the default choice for high frequency applications. It combines the shielding effectiveness of the foil shield with the flex life of the braid.
- Serve shields consist of wires wrapped in a spiral around the wires. Serve shields work great for low frequency applications. However, the spiral wrap creates a coil effect that causes issues for signals above about 1 MHz.
Importance of Cable-Connector Shield Termination
Good overall shielding effectiveness for a cable assembly is only achieved if the shield is properly terminated to the connector, on both ends of the harness. As a general rule, the overall shielding effectiveness will be dictated by the size of the largest opening throughout the assembly (the smaller, the better). This large opening most often occurs at the cable-connector transition. In order to address this, it is important to maintain a termination across the full 360° of the cable-connector mate.
Conclusion
Ensuring proper shielding is a critical part of nearly all cable assemblies. When designing a cable, there are several different options that should be considered. Understanding the options laid out in this article should help engineers design their cables to adequately address their needs. Contact Omnetics to learn more.
Did you know?
According to the United Nations Office for Outer Space Affairs, in history 8,126 objects have been launched into space, and over 22% of these are within the last eight years alone. In 2017, 453 objects launched into space, which equates to over 5% of the objects ever launched into space since the first ever satellite in 1957.
See Omnetics’ products optimized for space here.
Calendar of Events
25-27
Modern Day Marine
Location: Quantico, VA, USA | Booth #3004
Shared booth with Black Diamond Advanced Technology
3-7
Neuroscience
Location: San Diego, CA, USA | Booth #2033
13-16
Electronica
Location: Munich, Germany
27-28
SpaceCom
Location: Houston, TX, USA | Booth #235